Of all segments in the cannabis industry, cultivation may be the most competitive and complicated. There’s little room for error, and industrial-scale operations are starting to put pressure on smaller farms. Not coincidentally, prices for flower and biomass have been on a steady downhill slide in almost every cannabis-legal state.
In “the old days,” cannabis was grown on covert farms in the mountains or in nondescript warehouses in urban areas, but times have changed. With legalization, companies now may construct highly efficient, industrial-scale greenhouses that harness the power of the sun and fine-tune environmental variables in grow rooms the size of football fields. To survive in this intensely competitive side of the business, growers wisely turn to the traditional agricultural industry and academic institutions to look for answers, adopting and customizing technology tools and scientific methods that have been used on other crops for decades.
As the bigger-better-faster-more mentality takes hold, companies in the United States and Canada are in a race to build the largest cultivation operations in history, using every new and old trick in the book to maximize efficiency, sustainability, and production.
A canna-business park in the desert
Located in the Southern California city Desert Hot Springs, the Coachillin’ Canna-Business Park spreads out across 160 acres, staking a claim as the largest cooperative canna-business compound in the U.S. When completed, it will feature more than 3 million square feet of cultivation, manufacturing, processing, laboratory testing, distribution, and touring/education facilities.
Dr. Robb Farms is building seven facilities on the site. In total, the company will occupy 130,000 square feet of plant canopy and an additional 40,000 square feet of manufacturing space. The greenhouses have been engineered from the ground up to create a perfect playground for experimentation in plant science, with translucent roofs to let in sun and high-intensity lights; elaborate heating, ventilation, and air conditioning systems; and other technology that enables pinpoint control of environmental conditions in the cannabis cultivation rooms.
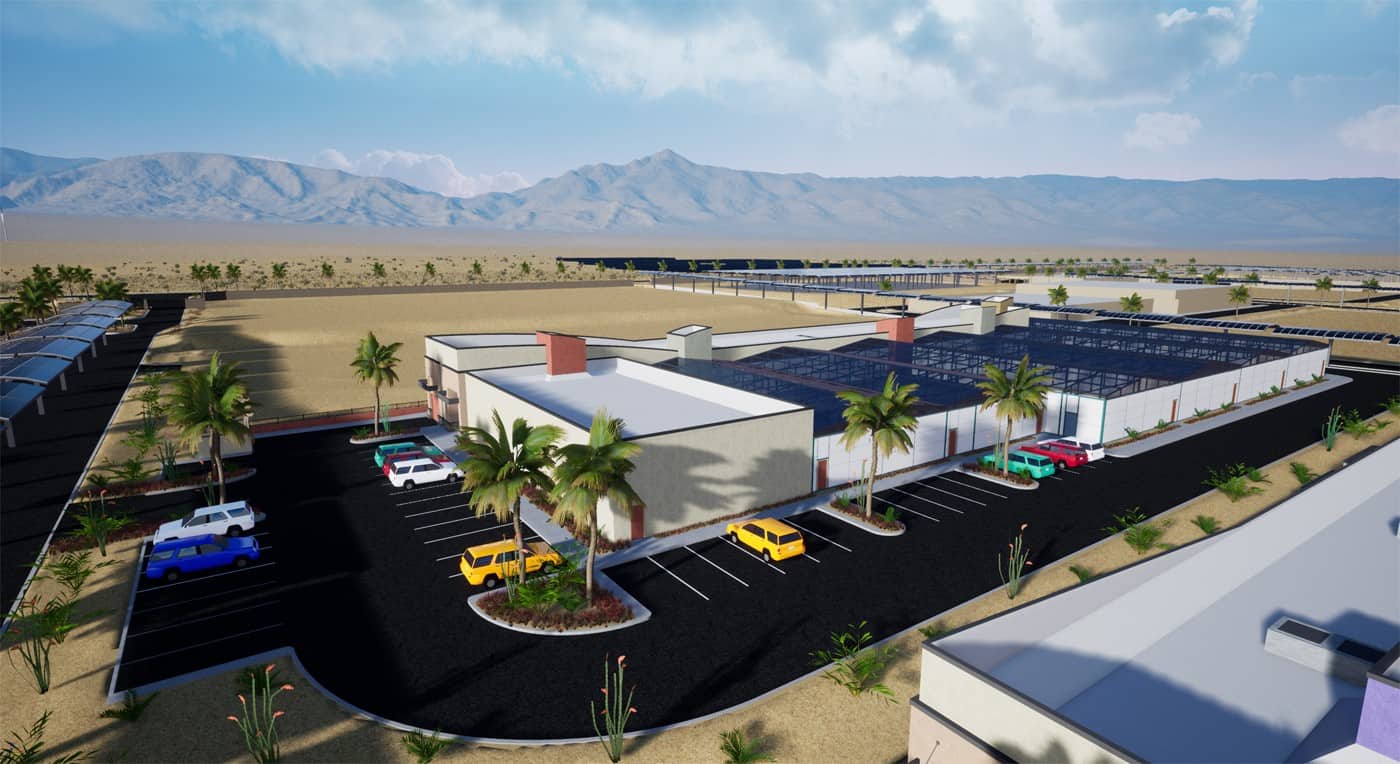
In just one facility, the company installed 780 tons of cooling capacity, making the space more closely resemble an indoor grow than a greenhouse. The space benefits from full-spectrum sunlight enhanced by LED and high-density lights that are meant to stimulate the production of complex combinations of cannabinoids and terpenes, according to Dr. Robert Flannery, the farm’s founder and chief executive officer.
Flannery earned a PhD from University of California, Davis, specializing in cut-flower production, among other things. He began working with cannabis in the late 1990s. One of the biggest trends in the agriculture industry currently, he said, is digital horticulture, which uses data and artificial intelligence to build mathematical models that project chemical profiles and yields, leading to more consistent and efficient grow cycles. “What’s great about these models is they can be built quickly and automatically and home in on these predictions,” he said.
He also noted that in the agricultural industry, increasing efficiency and sustainability is the name of the game, and the two pursuits go hand in hand.
“We are seeing an influx in technology come into the cannabis space, and the influx of capital will push hard on those new technologies. That will kick back into the food production world,” he said. “Companies will start growing more high-quality vegetable crops close to where they are consumed. There will be a back and forth between cannabis and the rest of horticulture, in controlling environments around plants as much as possible.”
East Coast cannabis
About 3,000 miles away, on the opposite coast, AmeriCann Chief Executive Officer Tim Keogh is building a 30,000-square-foot hybrid greenhouse in southeastern Massachusetts, in an environment that couldn’t be more different from Desert Hot Springs.
With a budget of $7.5 million, the facility will be loaded with high-tech design elements and is expected to produce 7,500 pounds of flower and 400,000 units of infused products annually. After partnering in an indoor grow in Colorado in 2014, Keogh said AmeriCann targeted Massachusetts as a promising market for a hybrid greenhouse project. He toured dozens of traditional greenhouses in the U.S. and Canada before his company designed a facility that can handle freezing temperatures through winter and hot weather in the summer yet produce consistent flower year-round.
Working with Bask Premium Cannabis, based in Fairhaven, Massachusetts, AmeriCann hopes to find about fifteen cultivars that will grow happily in its hybrid greenhouse environment. The structure employs customized systems across the board, from fertigation and environmental monitoring controls to security and odor mitigation (a system that was adapted from a hog farm). “We’re not expecting to take cultivars spoiled by indoor climates and move them into a greenhouse environment where we deal with outside air and natural sun,” Keogh said. “The data we collect will help us make decisions about which cultivars are best suited for our environment.”
Keogh estimated there is currently about 800,000 square feet of flower production in all of Massachusetts. He called current efforts to get lab-approved flower on the shelves a “frenzy.” Top-shelf varieties are fetching as much as $25 per gram.
Fine-tuning the grow
Based in Lafayette, Colorado, urban-gro has clients in most legal states in the U.S. and Canada. The company specializes in helping cultivators fine-tune and scale their operations while improving their ability to predict and repeat results. urban-gro’s ag-tech division, Soleil Technologies, develops customized sensors and imaging devices that help growers monitor and automate the critical variables in a cultivation operation: temperature, humidity, carbon dioxide, light intensity, nutrients, water quality, and more.
“When we deploy our system, the data is collected and comes in right away with real-time views and views over time, too,” said Larry Dodson, chief technology officer. “Based on the data, growers will start to make changes in fan speeds and directions, dehumidifier placement, and also in their dry and cure rooms. They see the value immediately in plant health, yields, and THC levels, and they also appreciate the reduction in scraps and waste.”
“With LED I’m starting to see less hesitancy and more acceptance, and new lamps coming out are tremendous and high quality,” Dodson said. “They are more expensive, but the advantages are becoming more clear. I’m not knocking HPS [high-pressure sodium], but they are limited in wavelengths, get hot, and have very high energy costs. If customers want LED, it is better for the long term, and the flexibility of that light is superior.”
LED lights allow growers to use spectrums outside the standard 400 nanometers to 700 nanometers range—the wavelengths that are visible to the human eye—going down into the 300s and up into the 700s, he explained. When applied in various stages of vegetative and flower development, the different wavelengths and photon energy have an impact on plants’ biomass and phytochemical development.
“Those wavelengths are available, but how they are applied and adjusted in the crop cycle is new,” said Dodson. “So, now we are making a multi-profile, multi-spectral light control solution as part of our overall technology offering.”
In its research and development lab, urban-gro also is creating new sensors and other environmental monitoring equipment it expects will be much less expensive while still delivering accurate results across large indoor and greenhouse cultivation rooms.
“One of our focuses as we develop more sensing and imaging devices is for growers looking for specific expressions, so they can repeat it with a particular cultivar,” Dodson said. “We think it’s fascinating and are looking for talented growers who can help our ability to develop the right tools for a precise level of control.”
Applied science and lab analysis
While new customized and automated technologies are a major focus for large-scale farms, sometimes more fundamental horticultural issues need to be addressed. Those center on hard science and analytical lab testing, resources cannabis farmers sorely lacked in the past.
When Graham Farrar noticed several plants in his garden were suffering last year, he and his staff couldn’t identify the problem or even decide what to call the affliction. Terpenes and resin development were coming to a halt during the flowering cycle. As they watched the buds turn a pale yellow, they dubbed the disease “yellow head.” As chief executive officer and founder of Glass House Farms on the Santa Barbara, California, coast, Farrar knew he needed to solve the problem quickly, before it spread any farther. Five years ago, most farmers in his situation might have whispered to a few neighboring farmers about ol’ yellow head, asking whether their colleagues had any ideas or potions to get rid of the menace. But last year, Farrar went straight to the best knowledge source he could imagine: a plant scientist at UC Davis, one of the best horticulture institutions in the country.
“He couldn’t give advice himself, but he referred me to an ex-student [Jeremy Warren] who already had a theory on it,” Farrar said. “Jeremy came down and we engaged him to take samples, and he used RNA sequencing to find the pathogen. Then we developed a test for it, and even confirmed tests for it on asymptomatic plants.” (Dark Heart Nursery recently identified the disease as “hop latent viroid.”)
Before long, yellow head was no longer a problem, and all is well at Glass House’s 500,000-square-foot plant canopy.
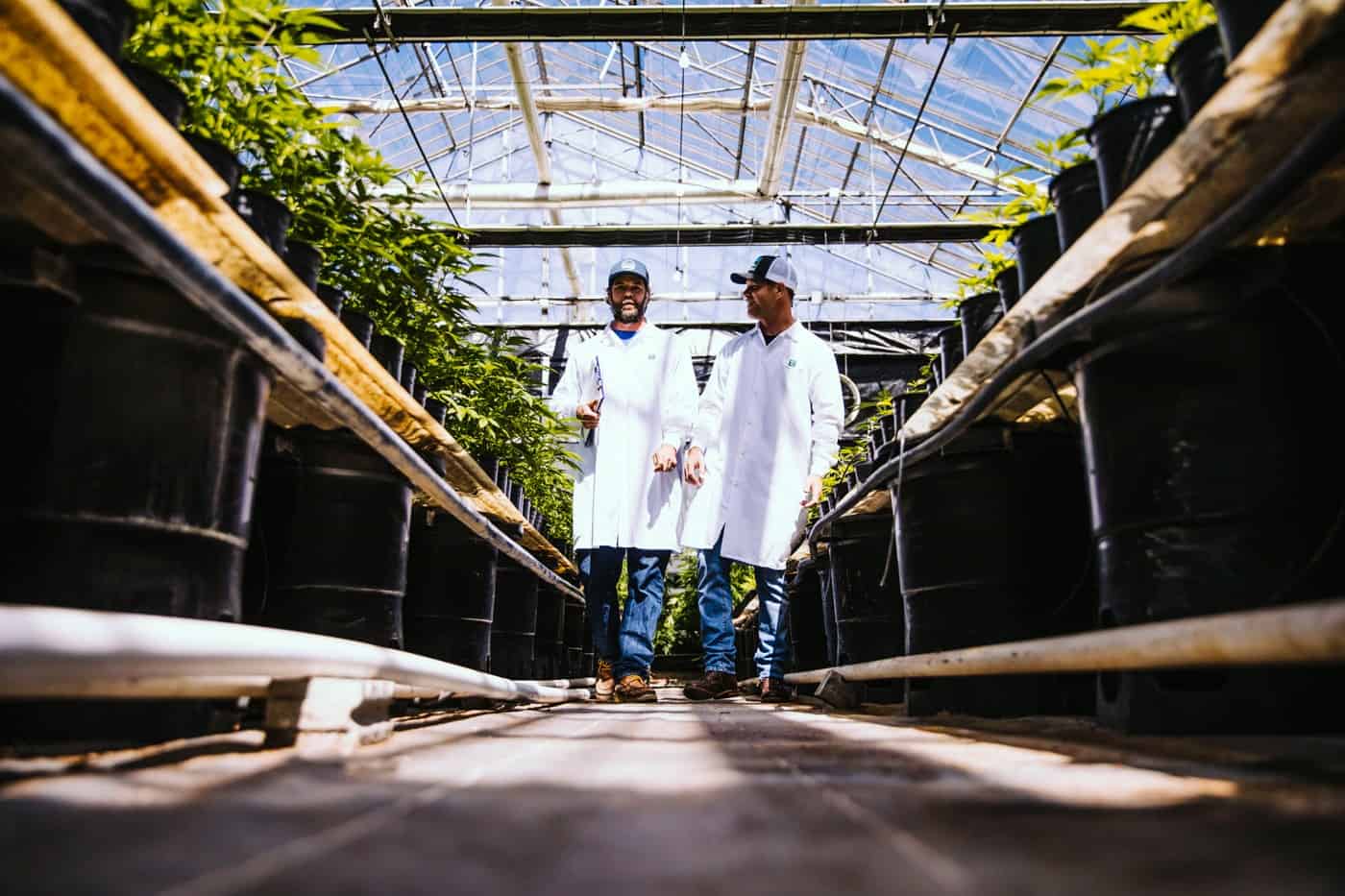
Until recently, farmers in the U.S. cannabis industry didn’t have access to basic agricultural research or applied science. The result: Little is known about the cannabis genome and the chemical makeup of thousands of landrace and crossbred cultivars around the world. Although research still is limited in the U.S., which presents a major roadblock to serious medical advances, cannabis cultivators are making advances of their own, incorporating science, research, data collection, and analytical tools into the daily grind on the farm.
“I see things in greenhouses that are diseases that haven’t been identified in cannabis, and oftentimes in agriculture it was the universities doing this work for strawberries and other crops,” said Warren, who serves as director of plant health at Dark Heart Nursery in Oakland, California. “So, now in cannabis we are discovering more pathogens and getting the stock clean, which will make a big difference in nurseries, farms, and greenhouses. If you get rid of the pathogens, other problems farmers had attributed to something else might go away.”
A two-way street
As new investment pours into the industry, the science and technology used to diagnose problems and streamline operations will put cannabis farmers in an unfamiliar position—aligned with the traditional agriculture industry and leaning on academics, scientists, and ag co-ops that have decades of experience improving the health of plants and crops in commercial production facilities.
urban-gro is developing new technology in lower-cost sensors to monitor crops, spectral imaging and sensing tools for identifying plant health issues, and for good measure, maybe some drones.
“For indoors in larger greenhouses it could be a good use of the [drone] technology,” said Dodson. “It might allow you to more easily deploy sensors and move them around in repeatable patterns. You could have just a couple in there instead of a few hundred.”
Just as traditional ag science and technology are helping cannabis farmers, some expect the knowledge to flow both ways as innovation occurs within the cannabis industry.
“Looking at a plant that produces 113 known cannabinoids, there are so many of these that we still need to explore,” said Flannery. “We’re seeing technology that can help regulate the enzymes that produce different cannabinoids, at higher concentrations, and that’s the stuff that gets my tail wagging. This is the future of ag in general, not just cannabis: being able to breed very quickly and provide products as efficiently as possible to the marketplace.”
[…] characterized by the presence of larger buds, dense branches, and a short stature. It also has a shorter flowering cycle than its sativa cousin. Indica cannabis often has high THC and has been harvested for centuries for […]
[…] characterized by the presence of larger buds, dense branches, and a short stature. It also has a shorter flowering cycle than its sativa cousin. Indica cannabis often has high THC and has been harvested for centuries for […]