The past five years of state-by-state legalization in the United States and beyond have brought sweeping changes to every area of the hemp and cannabis industries. New brands and products flood the marketplace daily, joined by a new generation of cultivators interested in trying their hand at growing hemp and cannabis in a friendlier, more legal landscape.
Many of the hemp and cannabis growing practices of the past thirty years were not based on what was the most cost-effective or efficient; rather, they were adaptation responses to the legal environment. Accordingly, today’s cultivation techniques are being overhauled by savvy cultivators and entrepreneurs maneuvering their systems for the highest-quality, lowest-cost product in a competitive marketplace. As most seasoned growers will attest, by far the most labor-intensive and expensive part of growing cannabis is the harvesting process. But recent developments in cultivation — especially autoflowering plants — support effective, low-cost harvest methods.
Historical perspective
In the Emerald Triangle and other legacy pioneering areas that supported medical cultivation, the common practice in outdoor cultivation was to have a low plant count, a large plant size, and photoperiod genetics that could be held in a vegetative state to achieve the desired massive plant stature. This was mainly due to per-plant medical license limitations that allowed people to grow a fixed number of plants for medical purposes. The shifting legal landscape has had a domino effect on horticultural practices.
As statewide recreational legalization and broader-scale commercial permits became available — first in the hemp space and later in early-adopter states like California, Oregon, and Colorado — innovators and cost-aware, systems-oriented growers began to change the cultivation landscape again to reflect more common agricultural practices. Thus, the legacy style of growing a limited number of large photoperiod plants needing specific light cycles, up-potting, specialized pruning, trellising with nets, and ladders has begun to give way to larger quantities of smaller, compact autoflowering or “day-neutral” plants. These plants can be managed in an outdoor row-cropping system with drip irrigation and tractor power and planted in manageable successions without any need for light cycle manipulation or control.
Current practices
In the current agricultural paradigm, tractors are by far the most effective way to bring down overall production and harvest costs. They allow rapid field prep, shallow cultivation, boom sprayers for integrated pest management programs, and yet-to-be-fully-utilized implements like stripper headers that minimize the need for hand labor in biomass harvests. Though stripper headers are not in common use yet, this is the inevitable direction for extraction models that supply the vape and edibles markets—which together compose the lion’s share of current market use. While it would take a team of ten workers three or four full days to harvest an acre of autoflowering plants by hand, a properly equipped tractor could do the work in an hour. Though biomass sorting and loss of trichomes must be accounted for in this system, it’s only a matter of time before it becomes the norm. Finally, leaning creatively into innovative speculation, it is highly possible labor-intensive steps like big-leafing can be mechanized with similar equipment found in the vineyard industry to remove leaves in the fruiting zone.
Because of the specialized nature of harvesting finished flower for the premium smokable market, this step likely will continue to be done by hand for the foreseeable future. The precision and delicacy needed to harvest high-quality tops while maintaining their trichomes and structure has proved difficult to mechanize. A compact plant row-cropping system also will bring additional cost benefits at the harvesting step, specifically because of its canopy efficiency or flowering-site-to-plant-matter ratio. The larger, trellised, and netted plants favored by many growers produce more plant matter to sort through by hand, and their abundant vegetative growth can obscure and stunt the growth of interior flowering sites. Additionally, plants with excess vegetative growth are more likely to restrict sunlight and wind penetration into the canopy, increasing the risk of botrytis. With smaller plants there is less area for non-performing buds to hide, and only a few cuts are needed per plant if it’s to be harvested solely for tops. A likely model for optimal cost efficiency would combine harvesting premium tops by hand with “lowers” mechanically harvested for extraction.
Looking to the future
As legalization expands, new opportunities will arise for enterprising market leaders to develop cost-effective production and harvest strategies based on traditional agricultural systems. The most likely model to reduce overall costs at the harvesting step will combine row-cropping, agronomically bred day-neutral varieties with a compact stature, mechanization, and hybridized harvesting methods that reduce the overall number of hand cuts needed per plant. Though many companies have made massive strides in their overall cost-effectiveness, there are many innovative leaps and bounds yet to be made in what is still, by most definitions, a very young industry.
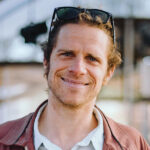
William Hancock is director of sales for Atlas Seed, which specializes in feminized, day-neutral (“autoflowering”) cannabis and hemp varieties bred for yield, mold resistance, and total cannabinoid content. The company was founded by seasoned wine grape, vegetable, and cannabis farmers in Sonoma County, California, who were searching for genetics that didn’t yet exist: uniform, stable, vigorous hybrids that would fit their existing agricultural model.